Precision mechanical alterations for your custom optical designs and specifications.
CNC capabilities include lightweighting, drilling, coring, edging, beveling, 3D contouring, and more.
Sydor Optics has the capability to manufacture complex shaped optics using our fleet of CNC machines from Haas and Fanuc. Our team has developed processes to machine an incoming blank to final size or machine an optic that has been fully polished without damaging the precision surfaces. This allows us to structure our job travelers to the best process that will allow us to manufacture our customer’s most demanding optics very efficiently.
Sydor Optics is home to a variety of CNC machines with varying capabilities and sizes. We have Haas VMCs (Vertical Machining Centers) ranging in size from the Mini-Mill to VF3-SSYT. These machines allow us to process parts from 12mm to 600mm is diameter or diagonal. We recently added 3 Fanuc Robo-Drill Model Ms to our stable of machines. These machines are compact, with high-speed spindles, and quick tool changes that have allowed us to have more efficient machining processes.
Through the partnerships we’ve established with our tooling suppliers, we can machine optics to our customers’ stringent requirements. Some of the features that we are able to machine include:
- Counterbores
- Countersinks
- Bevels
- Flats
- Notches
- Pocketing
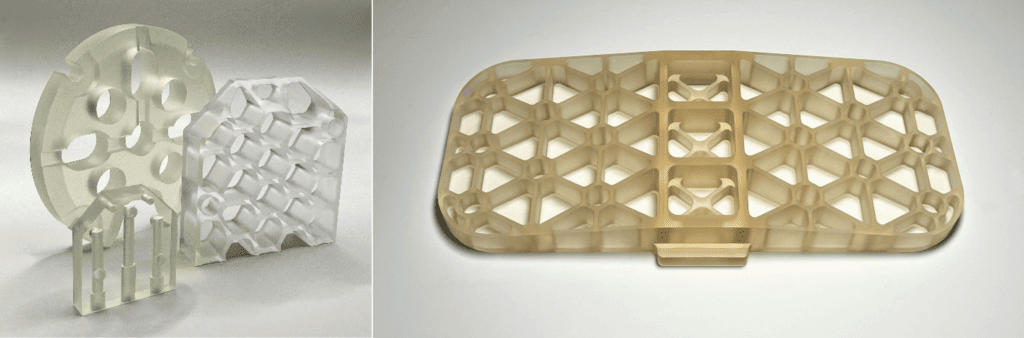
Light-weight optics are a specialty that we have devoted more resources to over the last few years. The design of these optics makes them challenging to machine because the wall thicknesses can be as thin as 2-3mm while maintaining superior flatness specifications. Ensuring that the optic survives the machining process requires precise programming, solid tooling, and the right setup to hold parts safely. We work very closely with our tooling suppliers to ensure that the diamond tooling is made to the precision requirements that is needed to successfully machine these complicated optics.
Case Study: Yield Improvement for CNC Machined Windows
Sydor Optics manufactures windows for a large defense customer that require unique shaping. We have been making these windows for years but wanted to make our CNC machining process more efficient and robust. An engineer was assigned to this project to work with members of the Manufacturing and Quality teams to update our process to ensure more consistency. Using the DMAIC process, he and the team made changes that standardized our process across all the windows that we manufacture for this customer. The following areas that were addressed for improvement were:
- Improved tooling
- Better surface protection
- Part handling
- Cleaning of the optics
After addressing these specific areas, the team was able to develop a revised process to ensure more consistent outcomes, as shown in the chart below. This has allowed us to better meet our customers’ increased demand with a more efficient process.
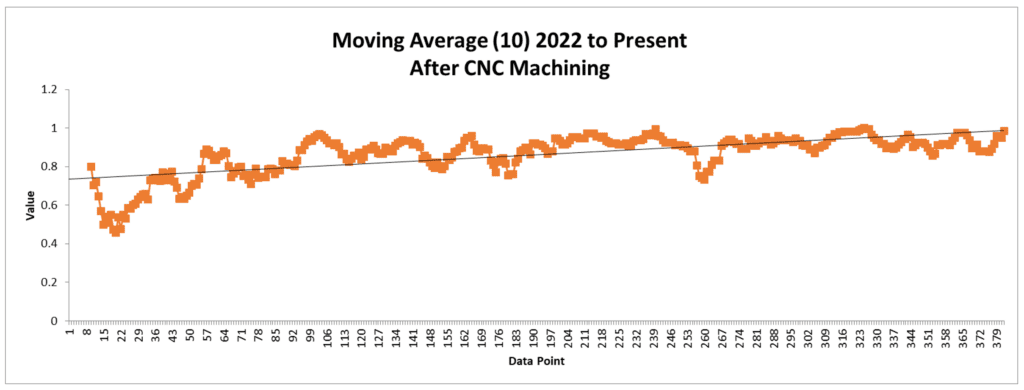