In an era where technological advancements are not just achievements but necessities, Sydor Optics remains at the forefront of the precision optics industry. With the establishment of the new Sydor Optics CNC Operations Center, we’re excited to announce significant upgrades and expansion to our CNC department. These advancements directly enhance our manufacturing capabilities, ensuring we continue to meet and exceed the evolving demands of our customers.
Our recent investments in cutting-edge CNC technologies and the development of our operational infrastructure demonstrate our commitment to innovation and efficiency. The new CNC Operations Center is not just a facility; it’s a testament to our dedication to quality and precision in manufacturing optics that power tomorrow’s technologies.
Investment in State-of-the-Art Technology
The recent acquisition of two groundbreaking CNC machines, the Method MV1100H and the Robodrill a-D21LiBadv Plus, underscores our commitment to maintaining a cutting-edge position in the optics manufacturing industry. These additions, one Method CNC and four Robodrills, all equipped with Fanuc controls, plus seven HAAS CNC machines with HAAS controllers increases our total production capacity to an impressive lineup of 12 advanced CNC machines.
With this robust fleet of CNC machines, featuring both Fanuc and HAAS control systems, we are better equipped than ever to meet the intricate and precise demands of our customers, reinforcing our role as a leader in the technology-driven future of optics manufacturing.
Advancements in CNC Technology
The recent enhancements in our CNC department represent a leap forward in our technological capabilities. With the Method MV1100H and the Method Robodrill a-D21LiBadv Plus, we are expanding our manufacturing capacity and elevating the standards of precision and efficiency in the industry.
The Method MV1100H features a larger bed for machining parts up to 550mm in diameter, combined with a higher spindle speed of 15,000 RPMs and a Big Plus dual contact spindle that enhances rigidity. Its 4th axis capabilities make it ideal for the complex part requirements of the future, aligning with our vision to tackle more challenging and intricate projects.
The Method Robodrill a-D21LiBadv Plus is known for its high spindle speed of 24,000 RPMs, and a more compact design while still accommodating up to 300mm diameter parts. Like the MV1100H, it boasts superior rigidity, ensuring that precision is maintained even at higher speeds. These machines exemplify our proactive approach to adopting technologies that anticipate the evolving needs of our industry for achieving tight tolerances, reducing cycle times, and improving the overall quality and efficiency of our production processes.
Key Features Across Both Machines
Both machines share several advanced features that set them apart in the CNC machining industry:
- High-Speed Machining: For faster production times without sacrificing quality, crucial for meeting customer demands for rapid delivery.
- Precision Engineering and Machining: Each machine is built to achieve accuracy within .0002” or 5 Microns, with repeatability of =/- .00008” or 2 Microns, ensuring that even the most stringent specifications are met.
- Advanced Controls: Equipped with industry-leading Fanuc controls known for their reliability and precision, to produce consistently high-quality parts.
- Enhanced Durability and Maintenance: Features such as stainless-steel covers and shields, and dual contact spindle tapers contribute to the longevity and durability of the machines, reducing downtime and maintenance needs.
- Automation Integration: Both machines are designed to integrate seamlessly with automation systems, enhancing our ability to handle high-volume jobs efficiently.
- Energy Efficiency and Environmental Consideration: Includes self-contained mist collection units and custom-made filtration units, emphasizing our commitment to sustainable manufacturing practices.
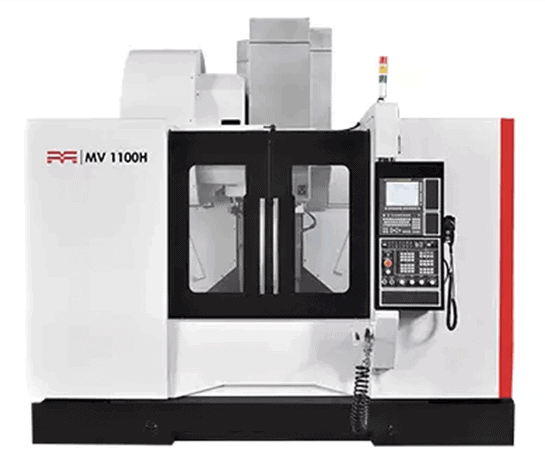
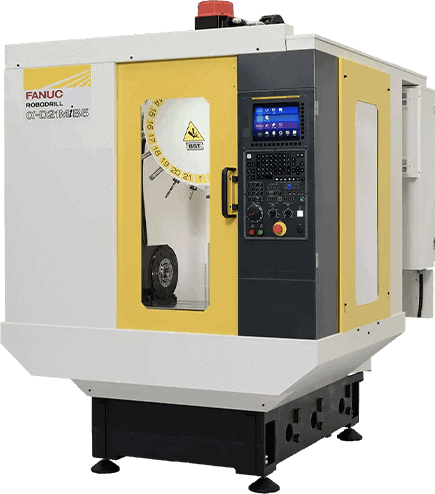
Join Us On This Journey
To our valued customers and industry partners, we invite you to experience the benefits of our new CNC Operations Center. Whether you have a challenging project requiring high precision optics or need reliable, quick-turn production capabilities, Sydor Optics is equipped to support your success. We are excited to collaborate with you to explore how our enhanced capabilities can meet your needs and exceed your expectations.
Enhancing Production Capabilities for High Demand, High Precision, High Throughput
The upgrades at Sydor Optics’ CNC Operations Center significantly boosts production capacity and efficiency, enabling us to excel in the high expectations of our customers through automation, customization, and operational efficiencies. Our facility is equipped to handle increased capacity and capabilities including:
- Expanded Production Volume: The new CNC machines allow us to increase output without compromising quality. This is crucial as we scale up to meet growing customer demands for high-volume, precision-manufactured optics components.
- Enhanced Machining Precision: The technological advancements in our machines enable us to produce components with tighter tolerances, which are increasingly demanded in sophisticated applications by our customers.
- Reduced Cycle Times: With faster spindle speeds and improved automation features, we can significantly cut down on machining time, enabling quicker turnaround times for projects. This efficiency is vital for customers who rely on swift delivery to maintain their competitive edge.
- Automation Features: Integrating advanced automation into our CNC processes means we can maintain high productivity around the clock. Automation not only increases efficiency but also helps in maintaining consistent quality across large batches.
- Custom Filtration Units: Each CNC machine is equipped with custom-made filtration units, ensuring the machining environment remains clean and controlled, which is critical for maintaining the integrity of precision components.
- Modular Tooling and Quick Changeover: Our continued use of modular tooling systems allows for quick setups and changeovers, greatly reducing downtime between production runs. This flexibility is key to adapting quickly to customer needs and handling a diverse range of projects.
- High Precision Quick Change Pallet Systems: These systems further enhance our flexibility and efficiency, allowing for rapid transitions between different production setups without sacrificing precision.
- Investment in Operator Interface and Machine Usability: Upgrades to the operator interface on our CNC machines make them more user-friendly and less dependent on formal programming skills, allowing our technicians to operate more efficiently and with greater autonomy.
Impact on Customers and Industry
The strategic upgrades to Sydor Optics’ CNC Operations Center reinforces our capacity for high-volume, high-precision manufacturing and underscores our dedication to driving industry standards forward. Through these enhancements, we aim to have a profound impact on our customers and the broader optics and technology industries.
Direct Benefits to Customers
- Tighter Tolerances and Higher Precision: With the integration of the latest CNC technologies, we are equipped to achieve and maintain tighter tolerances and higher precision in our products. This capability is crucial for customers involved in advanced technologies and industries where even minute discrepancies can affect overall performance.
- Quicker Turnaround Times: The efficiency gains from our new CNC machines translate into faster production cycles, enabling us to offer quicker turnaround times for our customers. This responsiveness is particularly valuable in industries where speed to market can be a critical competitive advantage.
- Customization and Flexibility: Our enhanced CNC capabilities allow for greater customization of products to meet specific customer needs. The ability to quickly switch setups and adjust production parameters means we can handle small batches and custom orders with the same efficiency as standard runs.
Shaping the Future of the Optics Industry Standards
Our investment in advanced manufacturing capabilities puts Sydor Optics at the forefront of flat optics design and production and helps build trust with our customers. They know that we can deliver on our promises of quality, precision, and delivery, making us a preferred partner in their ongoing and future projects through:
- Innovation in Manufacturing Processes: By adopting and integrating advanced CNC technologies, Sydor Optics will keep pace with industry developments and set new benchmarks for what is achievable in optics manufacturing. Our commitment to continuous improvement and adoption of cutting-edge technologies influences and elevates the standards within the industry.
- Supporting Next-Generation Technologies: The components we manufacture are integral to numerous technological innovations across various sectors, including semi-conductor, aerospace, defense, and healthcare. By enhancing our manufacturing processes, we ensure that our customers have access to the highest quality optics components necessary to drive breakthroughs in their fields.
- Sustainability and Efficiency: Our focus on automation, energy efficiency, and advanced filtration systems reflects our commitment to sustainable manufacturing practices. These efforts not only improve our operational footprint but also align with the growing industry and consumer demand for environmentally responsible manufacturing processes.
- Collaboration and Co-Development: We view our relationships with customers not just as supplier and client but as partners in innovation. By working closely with them to understand their specific needs and challenges, we tailor our processes and outputs to help them achieve their goals, fostering long-term collaborations that drive mutual success.