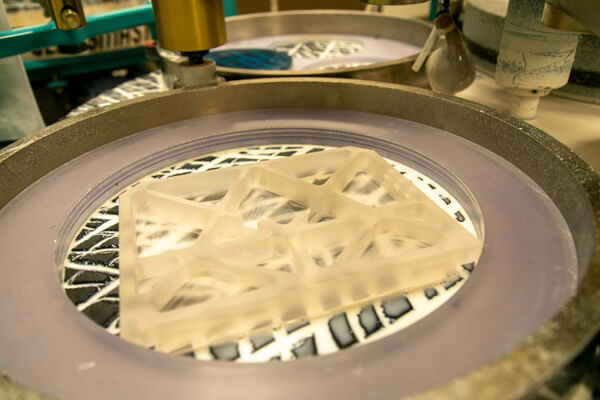
Surface Flatness
The highly skilled opticians at Sydor Optics have perfected the art and science of conventional pad and pitch polishing, also known as single-sided polishing. While surface flatness over a full clear aperture can be attained down to λ/20 PV, it is possible to reach surface flatness tolerances of λ/40 PV over smaller sub apertures.
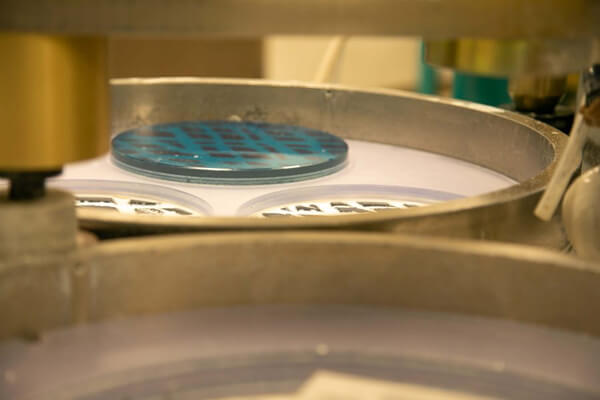
Surface Roughness
Opticians at Sydor Optics have passed down precision polishing techniques from generation to generation. Consequently, Sydor Optics’ proprietary techniques produce precision parts with surface roughness down to 3 Å RMS, ideal for laser applications requiring minimal scatter and maximum performance.
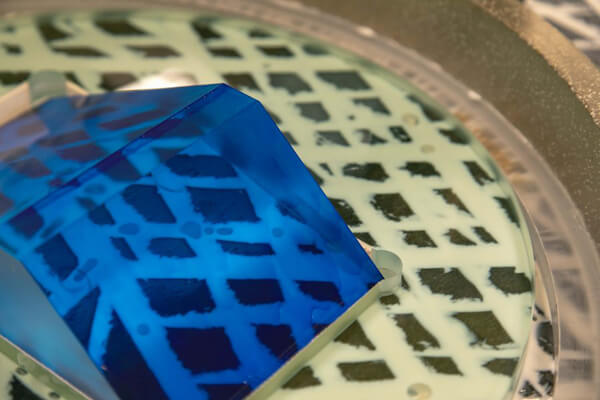
Cosmetics
Sydor Optics has years of experience producing precision-grade parts with cosmetics (scratch-dig) specifications as tight as 10-5, or as loose as 80-50. No matter the specified tolerance, trained metrology and inspection technicians at Sydor Optics are ready to verify that your parts meet the most rigorous quality guidelines.
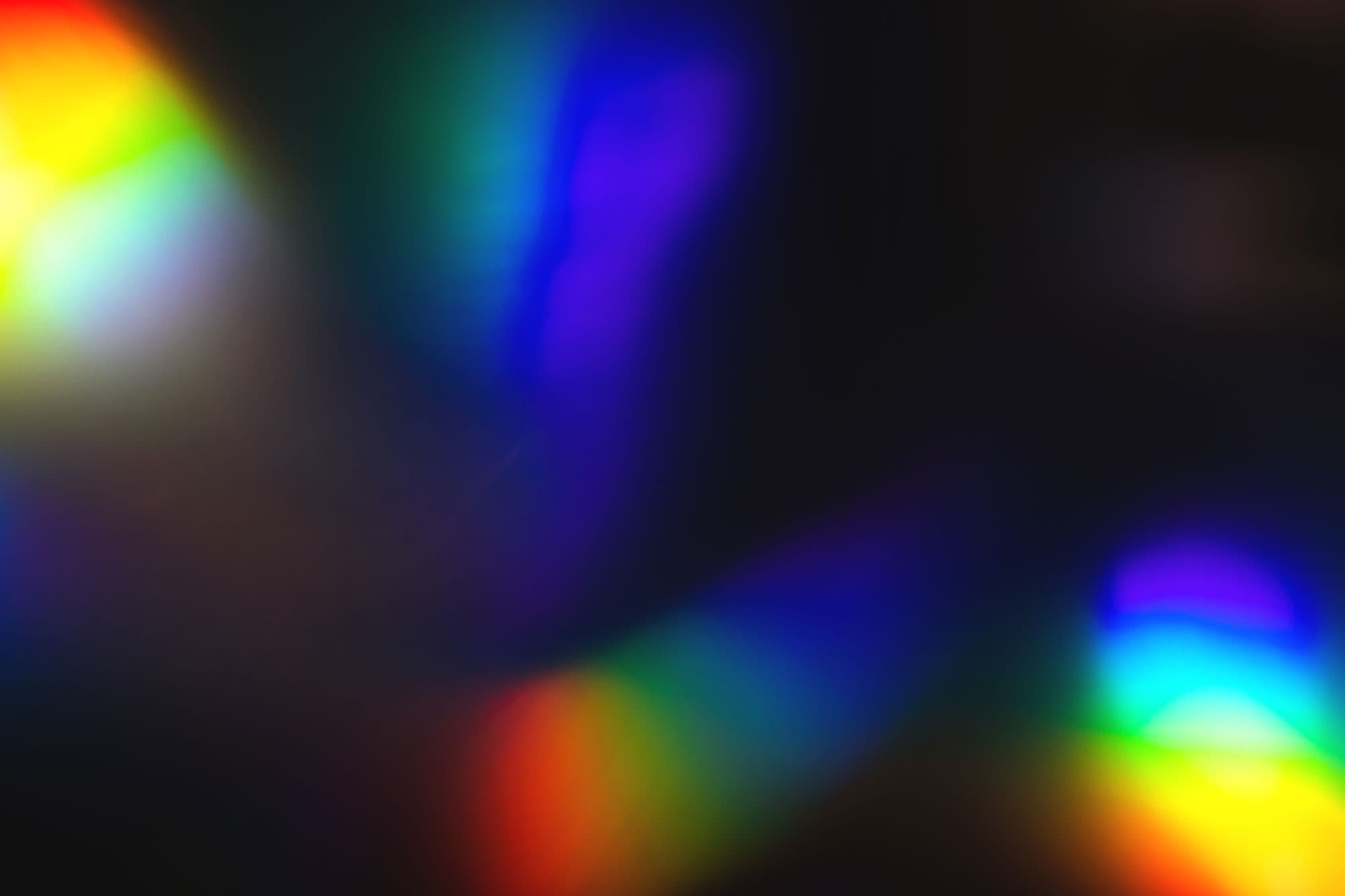
About Pitch Polishing
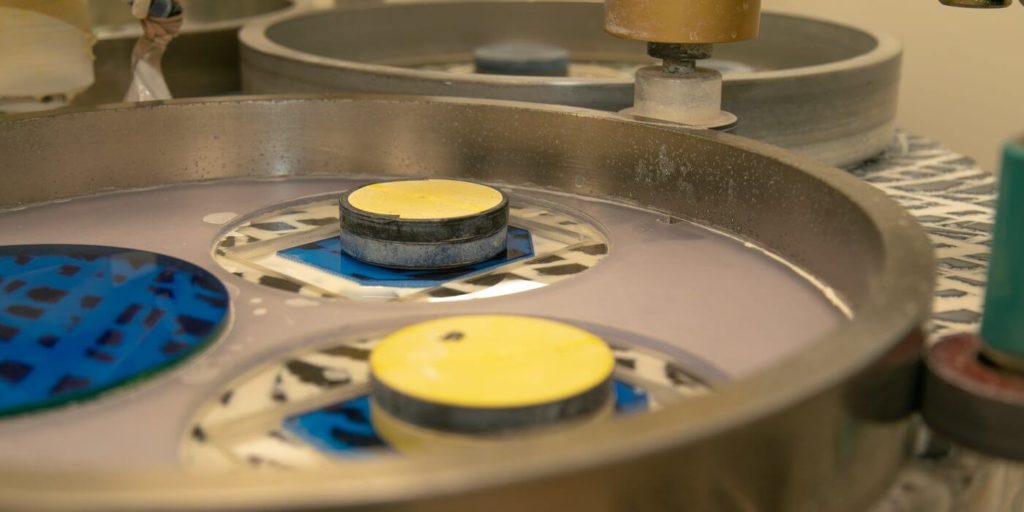
Precision Pitch Polishing
Pitch polishing is similar to the double-sided process except that it only polishes optics one side at a time. Sydor Optics frequently uses single-sided polishing machines for wedged optics, optical components thicker than 25mm and larger optics up to 750mm in diameter. The single-side process is typically used only if one side of an optical component needs to be polished, or if a part is too large for the double-sided process.
Pitch polishing involves significant skill and craftsmanship and can achieve much tighter tolerances for surface flatness, surface roughness, parallelism and cosmetics. Parts typically polished on a pitch table include optical flats and mirror substrates. Notably, the pitch polishing process also minimizes surface deformation on the edge of a part also known as edge roll.
Pitch tables are hand poured and have a semi-malleable surface with a consistency similar to roofing tar. Proprietary grooves are hand cut to allow the polishing slurry to flow beneath parts resulting in exceptional surface flatness and surface roughness. Pitch polishing is a non-deterministic trial-and-error process and combines both art and science. The highly-experienced opticians at Sydor Optics have an innate understanding of the optical glass polishing process and can provide consistent, high quality parts.
Optical Glass Polishing Manufacturing Limits
Specifications | Measurements |
---|---|
Diameter | ≤ 650mm |
Thickness | ≤ 100mm |
Length / Width | ≤ 350mm x 350mm |
Surface Roughness | ≥ 3 Å rms |
Parallelism | ≤ 5 arc seconds |
Cosmetics (MIL-PRF-13830B) | 60-40 to 10-5 |
Reflected Wavefront Error (RWE) – before coating | ≥ 1/20 wave over clear aperture |
Transmitted Wavefront Error (TWE) – before coating | ≥ 1/20 wave over clear aperture |
Wedge Angle Tolerance | ± 5 arc seconds |
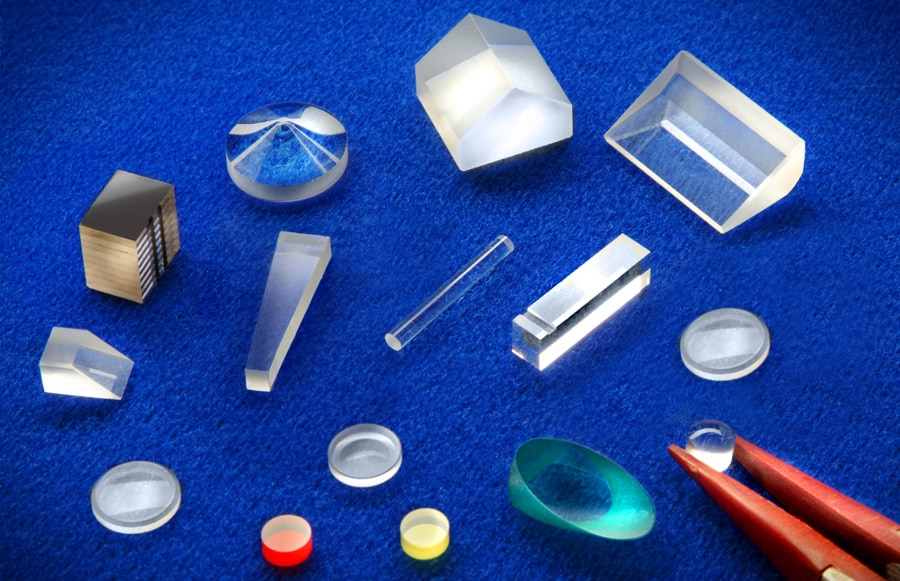