What are Optical Windows?
Optical windows, by function separate two environments for the purposes of either chemical, environmental, mechanical, thermal purposes, or a combination thereof. Windows range in a variety of sizes from just a few mms in diameter to meter-class optics. With optical windows, the key specifications involve transmitted wavefront, cosmetics, and dimensional requirements.
As larger windows are often used in outside environments, they are exposed to both the elements and contaminants which can negatively affect their surface. The good news is that in most cases these windows can be repolished, with a slight reduction in thickness and recoated for a considerable cost savings over buying new windows.
Weight is a major concern as this affects procurement of material (lead times and cost) to processing costs (handling, machining and polishing) to the coating (few coating companies can coat larger optics) and finally to the mounting in the intended application.
For this report we will consider anything over 300mm in diameter/diagonal and as large as extending to well over a meter. Optical windows can vary in both size and shape. They are popular in diameter format but also can be square or rectangular, with or without cropped or radius corners, or with the occasional need for elliptical or even irregular-shaped windows.
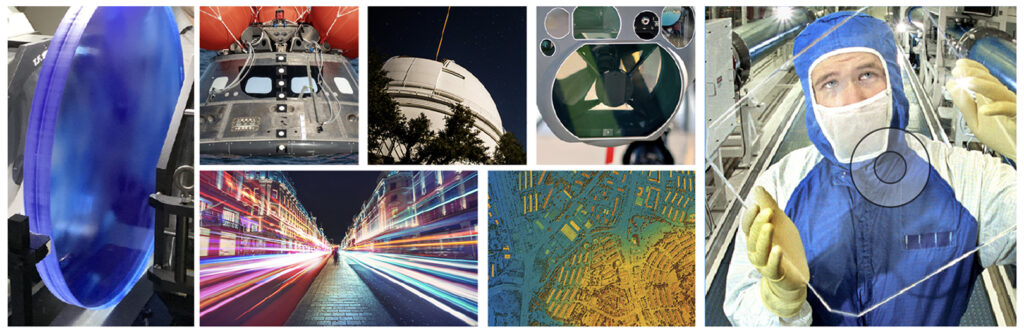
Large format windows are used in a wide variety of applications with a range of diversity in the criticality of these optics.
Windows can be used from small windows inside instrumentation to those used in aerospace – where failure can result in the loss of the aircraft/space vehicle and possibly the loss of life. For this article we will focus on large windows which are generally used in the following applications to name a few.
- Aerospace: space-based aircraft and habitats
- Astronomy: instrumentation and sensors
- Defense: aerial reconnaissance and laser-based defenses
- Free Space Optical Communication: laser communication
- High laser energy research: vacuum windows and debris shields
- LIDAR: atmospheric testing
The list of materials used for windows pales in comparison to the list of materials used in optical lenses.
For large format windows, we need a material that is transmissive for the wavelengths of use, has the homogeneity to achieve the transmitted wavefront to perform, and the anneal to ensure optimal stability.
Most popular materials used in the visible spectrum are: BK7, Borofloat®/Supremax® and Fused Silica. For the IR spectrum options include germanium, silicon, zinc selenide and zinc sulfide. Borofloat®/Supermax®, limited to 2-inch thickness is the least expensive and has relatively low expansion. N-BK7/SBL-7 is the next least expensive material and is a good option where heating and cooling are not an issue.
Fused silica is considered one of the best optical materials as it has very low expansion. Fused silica is the material of choice for large windows in Internal Confinement Fusion (ICF) given its ability to meet low birefringence and exceptional index homogeneity specifications over very large sizes.
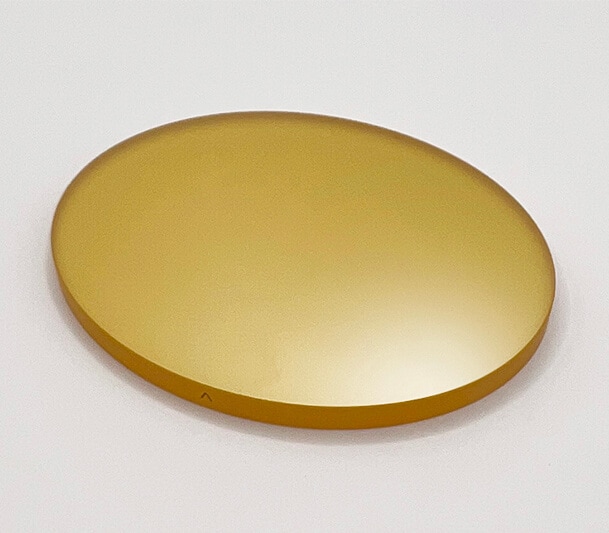
Of importance to both cost and results is the method of polishing.
For single pieces, single-side polishing is employed. As the name implies, one surface is polished at a time which can be time consuming and therefore costly. For larger quantities, double-side polishing is the optimal polishing process for both transmitted wavefront and cost.
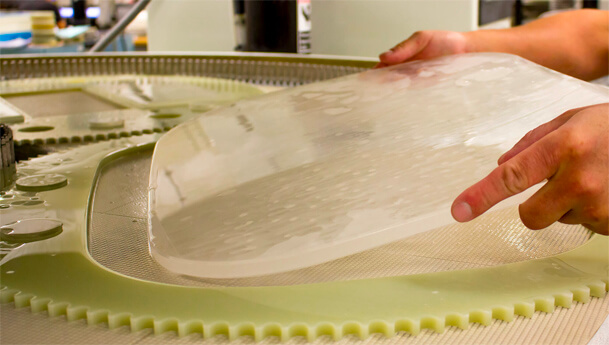
Transmitted Wavefront Error (TWE) specification is perhaps the most critical for windows and should match how the component is used.
The clear aperture including any sub apertures are important to specify accurately as it would be ineffective and potentially too costly to specify the entire clear aperture when the beam is smaller in size and scans the entire clear aperture. Especially in relation to the clear aperture and potential subapertures as smaller beams may be involved that translate over the entire clear aperture. Coupling TWE and slope specifications may involve additional surface figuring technology and therefore additional costs.
Testing transmitted wavefront on large windows is best performed with phase-shifting, large aperture interferometers. With larger interferometers one is able to capture full aperture interferograms which more completely characterize the entire surface as opposed to studying multiple interferograms of subapertures.
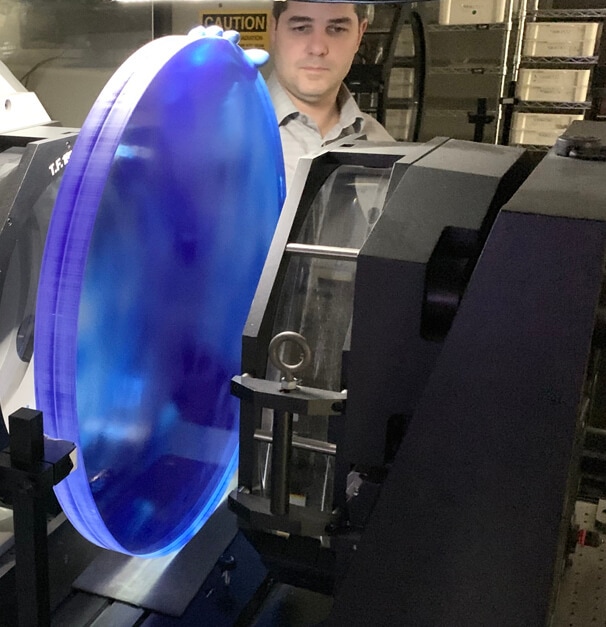
Coating and shipping considerations.
Large windows typically have AR coatings to improve their performance with additional coatings as optional such as those with oleophobic or hydrophobic qualities. Coating uniformity is critical since uniformity variation would cause the deposited filter coating to shift in wavelength space and likely be out of specification in some parts of the clear aperture. Uniformity challenges are dependent on many factors such as the deposition technique, deposition chamber size and geometry, distance from the parts to be coated to the source, and tool motion (e.g., planetary rotation, single axis rotation). Part shape (e.g., radius of curvature), surface roughness, and features such as holes or channels will also cause thickness uniformity variations. A broadband coating for instance can tolerate more nonuniformity compared to a high-performance AR V coat. Coaters can utilize a uniformity/shadow mask that is uniquely designed for a specific chamber to even out the coating thickness variation across the diameter of a large window.
Large windows are usually shipped in hard cases with the intimate packaging being as simple as tissue wrapping and bubble wrapping to protect the optic, or as complex as reusable Pet-G containers packed and sealed in a cleanroom environment.
Windows are often used as the final optical component of an optical system and the final protection or separation of environments may not be as specification critical as the other optics in the system but are nonetheless still important.
Inquire About Custom Flat Optics Capabilities
If you have more complex flat optics needs, we encourage you to contact our sales engineers using the form here to talk about your needs.
When we talk, our conversation will include topics such as:
- Can this be designed at a lower cost?
- Is this solution going to perform as optimally as required in the application’s environment?
- Where can Sydor apply our collective knowledge to enhance this design and your product?
- Is this design ideal for manufacturing?
Sydor is a trusted provider of design & manufacturing solutions for engineers who work with flat optics.
Consider our experience & expertise for your new or existing programs.
"*" indicates required fields