Subsurface damage can determine the effectiveness and lifetime of the optic within the system or assembly.
The ability to mitigate subsurface damage is very important for the performance of optical substrates, such as windows, lenses, and mirrors, especially when used within high power laser systems.
At Sydor Optics, we have over 60 years of experience in perfecting processes that are specifically designed to greatly minimize subsurface damage for optics used in these critical applications.
The most common types of initial surface preparation are band saw, rotary surface grinding, single side grinding, and double side grinding. Generally, the surface of an optic will experience multiple forms of surface preparation to achieve the final part specifications as illustrated in this graphic.
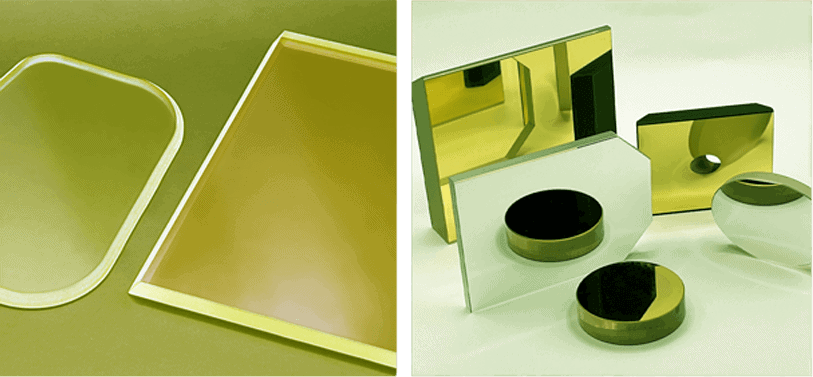
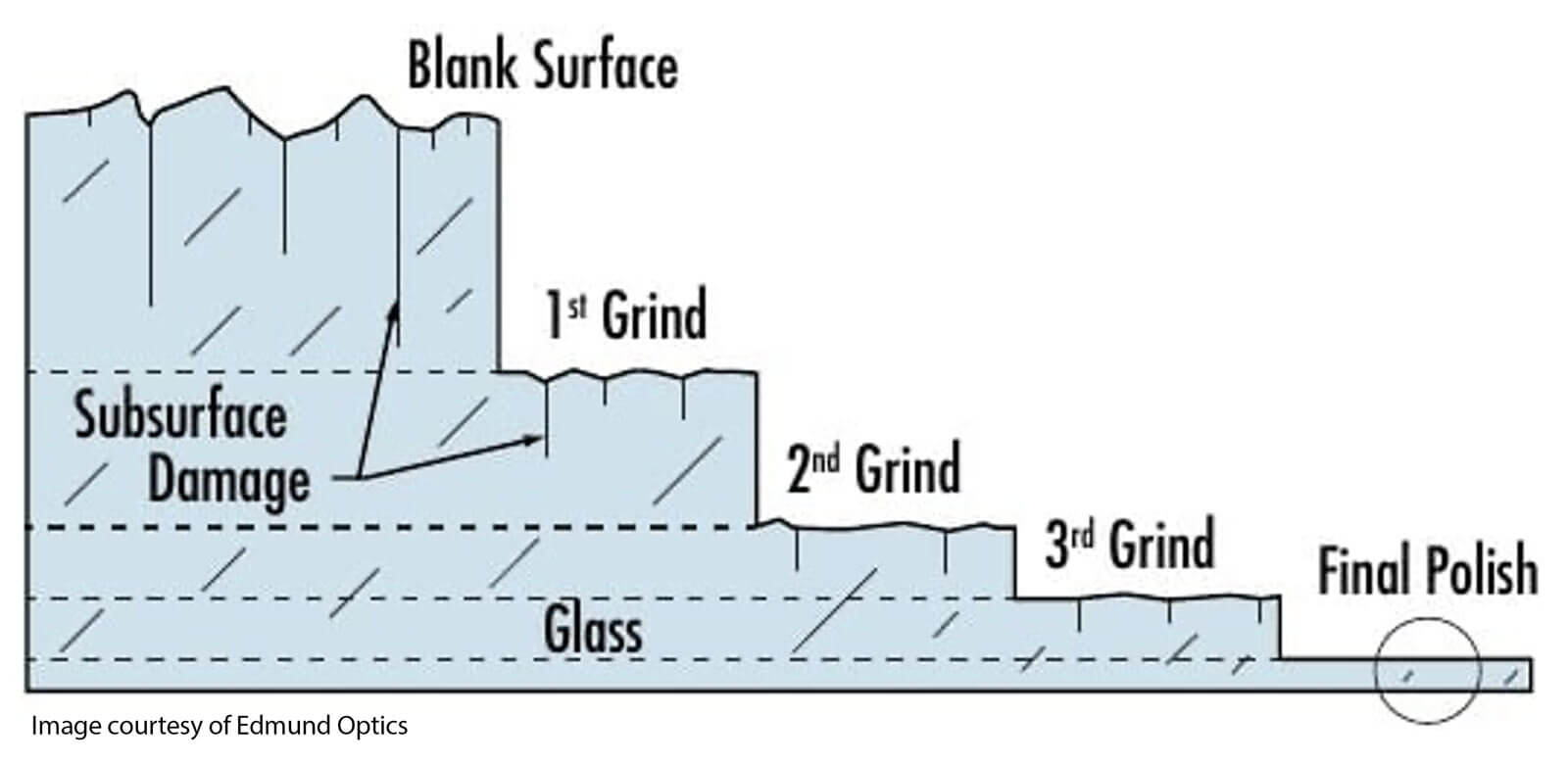
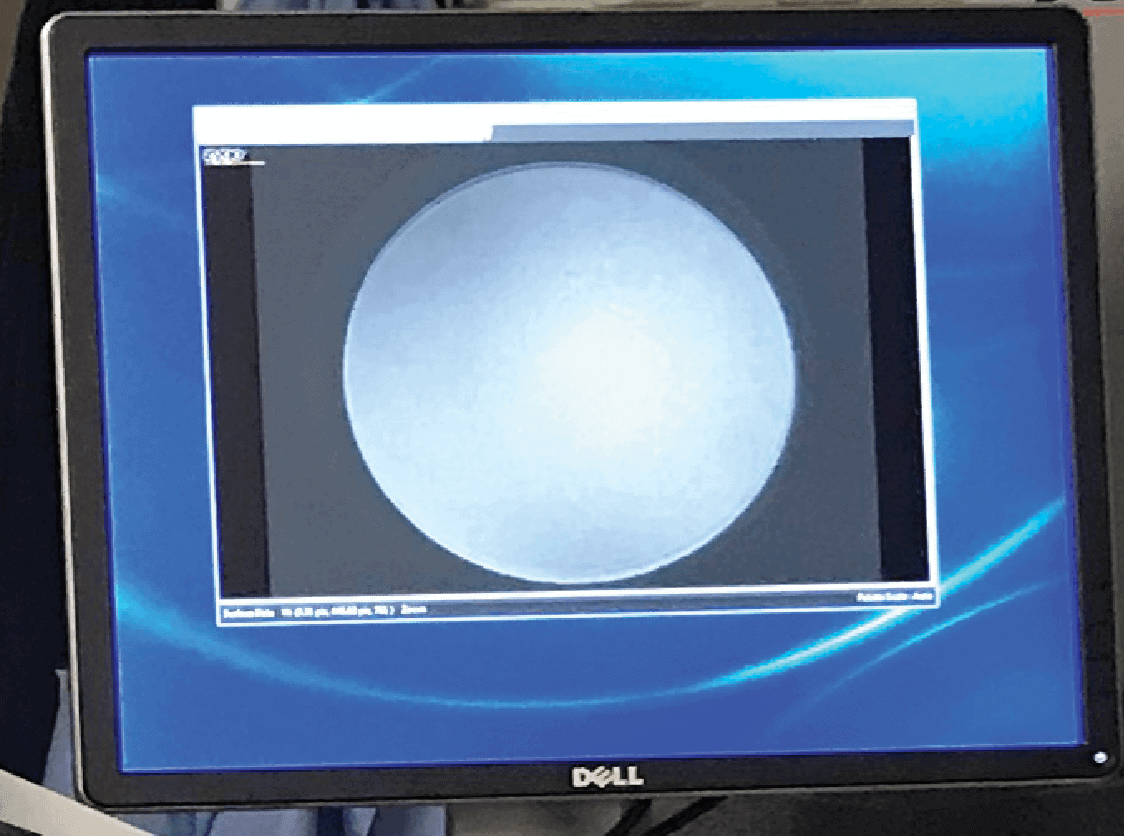
The Larger the Particle Size, The More Subsurface Damage
The amount of subsurface damage created is proportional to the size grinding media used in these surface preparation techniques. The larger the particle size, the more subsurface damage that is created during that process. Therefore, a 60-micron particle will create more subsurface damage than a 30-micron particle.
Measuring the amount of damage created can be done in several ways. The most common ways to evaluate subsurface damage are using an optical microscope, fluorescence spectra analysis, acid etching, and theoretical models. These methods have varying levels of effectiveness and may only approximate the damage created during the prior surface preparation.
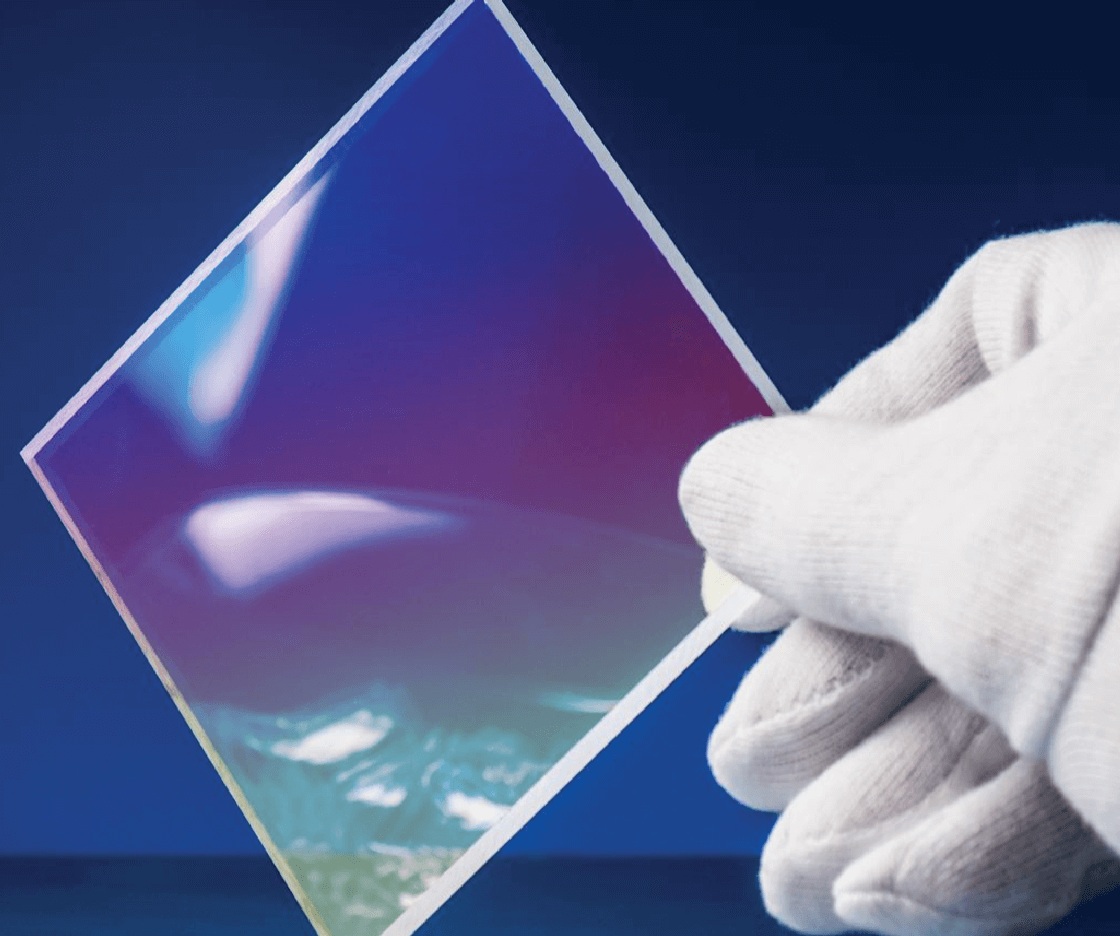
Mitigating Subsurface Damage Specifically for Laser Quality Optics
For laser quality optics, surface roughness/flatness and wavefront error are not enough to judge how an optic will perform and how long that optic will last in its application. This is where removing the subsurface damage created from each processing step is important. The general rule of thumb for precision optics processing is to remove three times the particle size used in the previous processing step. This means that if a 45-micron particle was used, 135 microns of material should be the minimum amount of material removed from the surface of the optic. This is widely known as the “3X removal method.”

The Final Polish for a Precision Surface
Multiple polishing methods will also follow this procedure to ensure that the grinding damage is fully removed. A pre-polishing step for initial material removal can be used with a polishing slurry that is greater than 1 micron in size and a polishing pad that will help shape the surface as needed. This can be done either using a single or double side polishing process. A final polishing step will then be used to bring the reflected or transmitted wavefront into specification. This step would include a soft polishing pad or pitch process to create a low roughness, precision surface with minimal subsurface damage. With our significant experience in processing optics, Sydor Optics has developed specific processes that ensure the optimal parameters to remove subsurface damage for use in high energy laser applications throughout the world.
If you have any questions about how Sydor Optics can help make optics with minimal subsurface damage for your application, please reach out to one of our Sales Account Managers.