Sydor Engineers, in collaboration with NYSP21 and RIT, dramatically reduce solid waste using innovative solid suspension process method.
Here at Sydor Optics, we strive to be good stewards of the environment and corporate neighbors. In an effort to better manage the wastewater that exits our facility, we entered into a project with the New York State Pollution and Prevention Institute (NYSP2I) at Rochester Institute of Technology (RIT) to evaluate the processing fluids in our double side grinding and CNC machining work centers. The processing fluids in these areas both contain high levels of solids, and they need to be removed before entering the public wastewater system.
In parallel with the project that was initiated with NYSP2I, our Principal Engineer started a project to help eliminate the solids in the CNC machine before these the fluids were changed over and discharged. The current operations of both departments knew there was opportunity to further reduce excess solids from the processing fluids before disposal. Our engineer designed an agitation system to ensure that the solids stay in suspension during operation so that they could be removed using another method. See the picture below of this system installed in the coolant tank of one of our CNC machines.
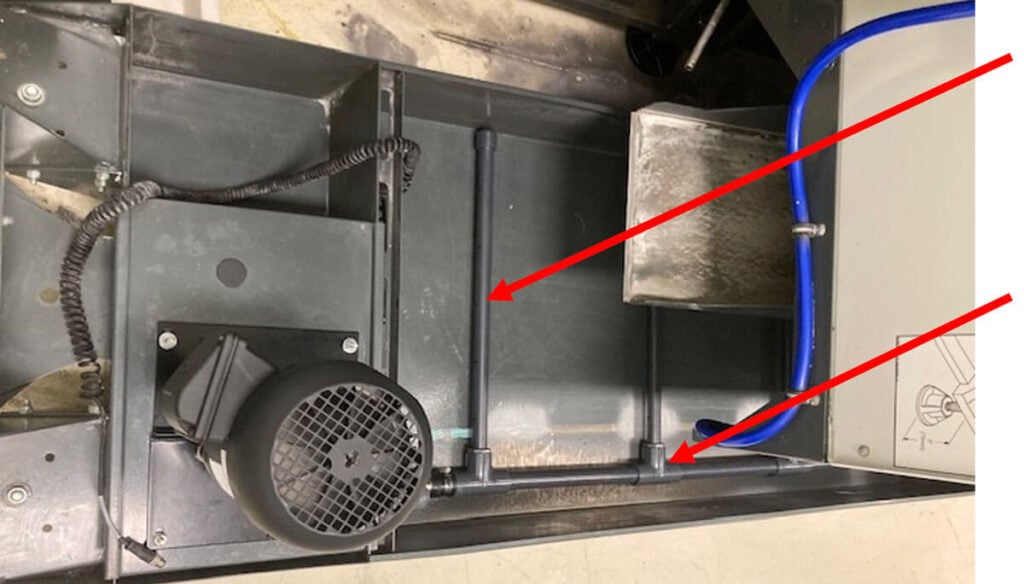
With the solids remaining suspended in solution, they can be more easily removed by utilizing different filtering techniques. This accomplished the goal of successfully removing a significant amount of solids from the coolant, by greater than 90%, and this had other positive impacts on our process:
- Cleaner coolant passing through the machine which leads to less wear and tear on the machines.
- Less downtime and labor cost for machine coolant change and tank cleanout. This would generally be performed once per month and take an entire work shift.
Because of the changes made through the internal project in the CNC department, the group at NYSP2I was able to concentrate on solids reduction in the double side grinding department. In working through this project with their team, we were able to make some additional changes that decreased the solids entering the machine during the lapping operation. This was accomplished by changing our coolant reservoirs. The new reservoirs provided 2 advantages over the previous tanks that were used.
- Larger reservoir to increase the amount of coolant available for the lapping process.
- The new tanks included a catch tray and baffle to allow solids to settle in multiple locations, while also having “cleaner” coolant available for use.
These changes provided instant savings by increasing the coolant changeover period from 2-3 days to 2-3 weeks with no adverse impacts on the results of our lapping operation. For the year, this amounted to savings in coolant volume and cost of about 70%. In addition, the amount of solids discharged from our facility has been substantially reduced by implementing the changes described above. The chart below shows the level of solids detected in our wastewater during quarterly testing.
The team at NYSP2I continued setting up tests and running experiments to better understand the generation, accumulation, and discharge of solids throughout our double side lapping operation. Once all the data had been collected, their team was able to make informed and detailed recommendations for the treatment of the process fluids in this operation.
Based on these suggestions, we will now move forward with implementing a solution that will remove even more solids from our outgoing waste stream.
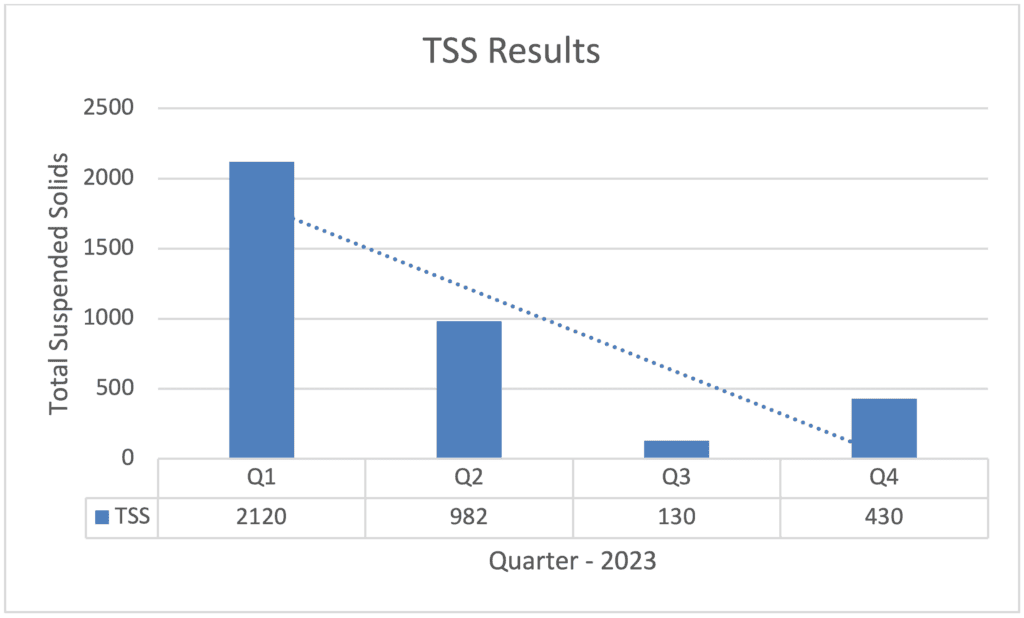